商用電気自動車を開発・販売するEVモーターズ・ジャパンが、北九州市内に独自の生産工場を建設中です。今回、徐々に生産設備が整ってきている現場を見ることができました。EVモーターズ・ジャパンが描く工場の将来像はどのようなものなのでしょうか。現地レポートをお届けします。
※この記事はAIによるポッドキャストでもお楽しみいただけます!
工場を併設した「体感型EV複合施設」
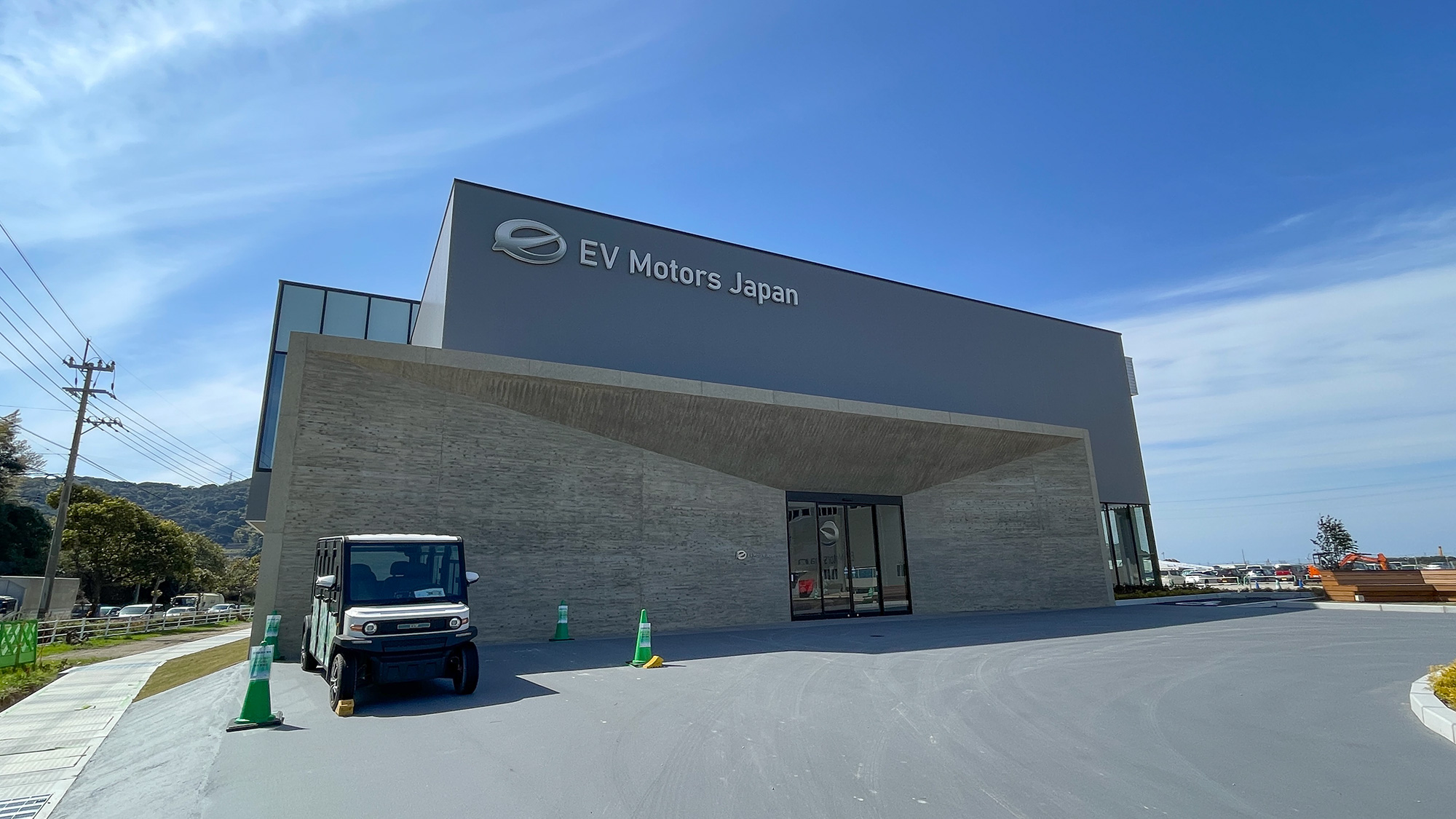
真新しいオフィス棟。
2025年3月下旬のある日、福岡県北九州市にあるEVモーターズ・ジャパン(EVM-J)本社にお邪魔しました。取材の目的は、ひとつは建設中の工場の様子を見ることで、もうひとつはEVM-Jの現在について、佐藤裕之(さとうゆうじ)代表取締役社長の考えを伺うことでした。
冬が戻ってきたかのように気温が下がった日でしたが、佐藤社長の話は熱く、工場の将来像に関しても具体的に姿が見えるもので、ちょっと身体がポカポカしました。そんな佐藤社長のインタビューは別の記事でお届けするとして、まずはEVM-Jの工場の様子からお伝えしたいと思います。
EVM-Jは、これまでEVsmartブログでも何度か紹介してきたように、商用電気自動車(EV)を中心に、開発、販売を手掛けるメーカーです。これまでは自社開発の製品を中国のOEM先に委託して生産するファブレス方式で、電気バスや急速充電器などを市場に供給してきました。
けれども数年前から自社工場の建設に着手し、独自生産を目指して動いてきました。当初の目標では2023年中の生産開始でしたが、生産、販売に必要な認証を取得するのに時間がかかったことなどもあり、2025年度内の生産開始を目指しています。
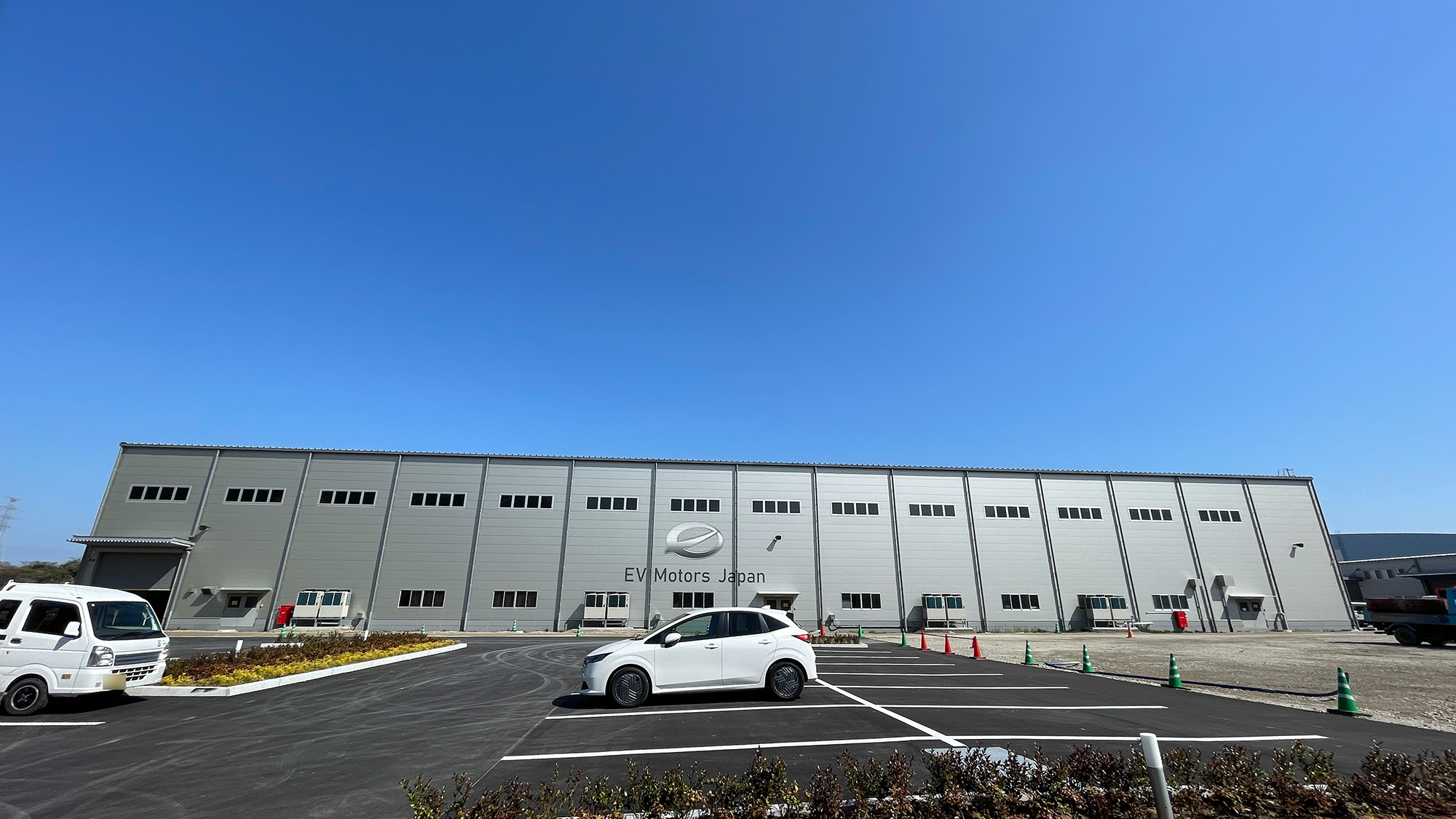
組立棟は東棟が完成済み。
工場全体の建設工事は全4期まであります。このうち第1期工事が完了した2024年12月に、関係者にお披露目を行いました。
EVM-Jの施設は、工場といっても単に製品を作るだけではありません。「ゼロエミッション e-PARK」と名付け、将来はソーラーパネルや風力発電による再生可能エネルギーで工場を稼働させることを目指しつつ、EV関連の技術展示をするスペースを設けたり、工場見学やEVの試乗などができる、工場を併設した”体感型EV複合施設”にすることを計画しています。
今回の取材で、そんな計画の一端を見ることができたのでした。
【関連記事】
「EVモーターズ・ジャパン」の心意気~電動化は脱化石燃料を実現するための日本の生き残り戦略(2022年8月6日)
EVモーターズ・ジャパンが新型EVバス3車種を発表/来年春ごろ予定の本格試乗が楽しみです(2024年11月1日)
完成すると年間1600台を生産可能
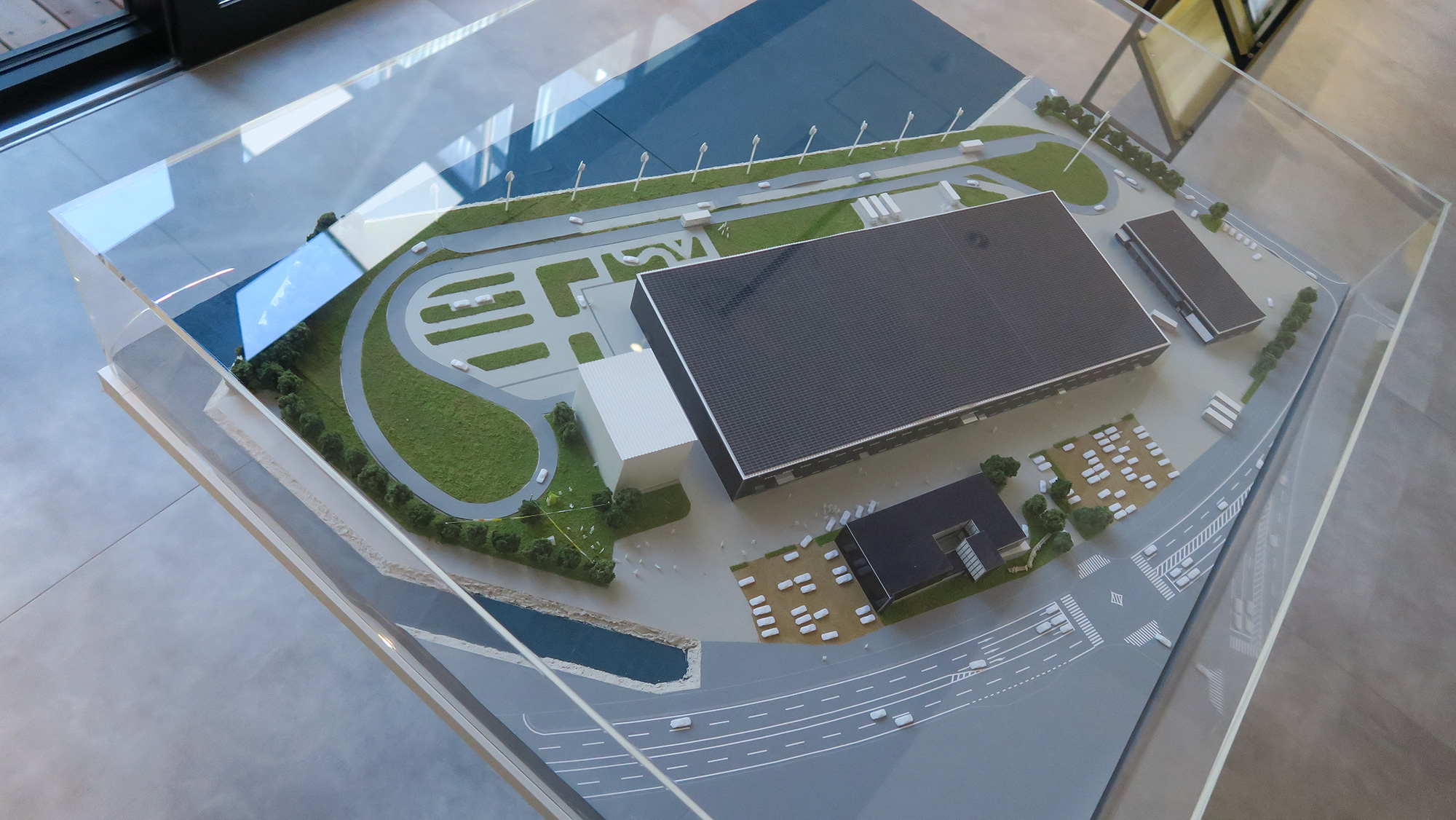
オフィス棟に完成模型が展示されていました。
ゼロエミッション e-PARKの総面積は約5万8000平方メートルで、車両の本社機能や資料館が入るオフィス棟、車両生産を行う最も大きな建物の組立棟、入荷後および出荷前検査を行うデバッグ棟のほか、試運転コースが設置されます。
このうちオフィス棟、試運転コース、デバッグ棟の建屋は完成しています。組立棟は第2期工事まで完了しています。オフィス棟完成の後、2025年3月には本社機能をゼロエミッション e-PARKに移転しました。
3期、4期の工事では、塗装設備の増設をしたり生産設備を拡充させていくほか、自家発電設備を導入予定です。現状の生産能力は年間160台ほどですが、完成時には1600台にすることを目指しています。
今回、見学できたのは、オフィス棟、デバッグ棟、組立棟です。また試運転コースは、EVM-Jのバスに「乗客」として乗りこんで体験することができました。
まず、オフィス棟に伺いました。建物は2階建てで、正面入口横にインバーターやeアクスルなどのEVに関するパーツを展示する予定です。ゼロエミッション e-PARKでは資料館だけでなく組立棟なども、申し込めば見学できるようにする計画です。
GPSで車両も作業用工具も管理
次に入ったのはデバッグ棟です。車両重量計測、ブレーキ検査やスピードメーター検査をはじめとして、車の車検のためのチェックをする装置が揃っています。
デバッグ棟で検査をする車両には電波を発するタグを付けて位置と車台番号を管理し、どの車両がどういった検査をしているのかを把握することができます。それだけでなく、作業に必要な工具の位置情報も3次元空間の中で、100mm単位で把握可能で、これにより工具の動作設定も管理することができるそうです。
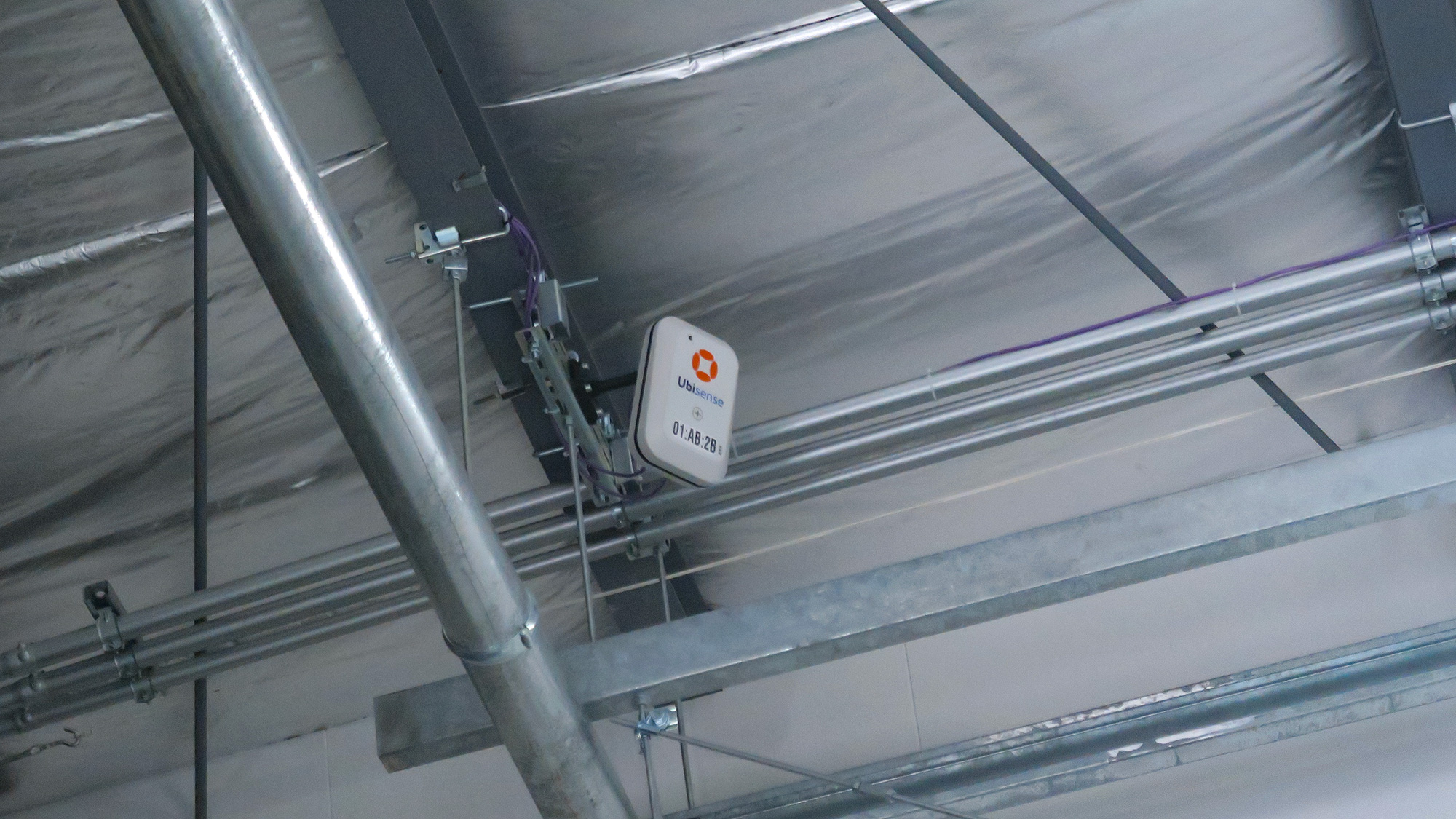
位置情報の計測器。
例えば締めつけ強度を一定にするトルクレンチは、車両の種類によってトルクを自動で変更することができます。人為的なミスを防ぐと同時に、作業の効率向上にもなります。
検査棟の奥にはEVM-Jが販売している急速充電器が置かれていました。また検査中のバスの裏には、充電器の出力を手動で変更できるテスト用の急速充電器もありました。テスト用充電器には手書きで注意書きが書いてあって、検査の臨場感を醸し出していました。
ロボット掃除機のような無人搬送車で車体を移動
次は組立棟です。組立棟は完成すると、幅72m、全長170mになります。ゼロエミッション e-PARKでは、大きさも種類も違うさまざまなタイプのバスの生産を同じ作業場所で行えるよう、新しい装置が導入されています。
ゼロエミッション e-PARKは通常の自動車工場のように組み立てる車両がどんどん流れていくライン生産方式ではなく、1か所である程度まとまった作業をするセル生産方式を採用しています。
この時、工程に応じて組み立て中の車体を移送するために、2台の無人搬送車(AGV)を同期して動かすシステムを導入しています。大型の車体は2台、小型なら1台で搬送できるようになっています。
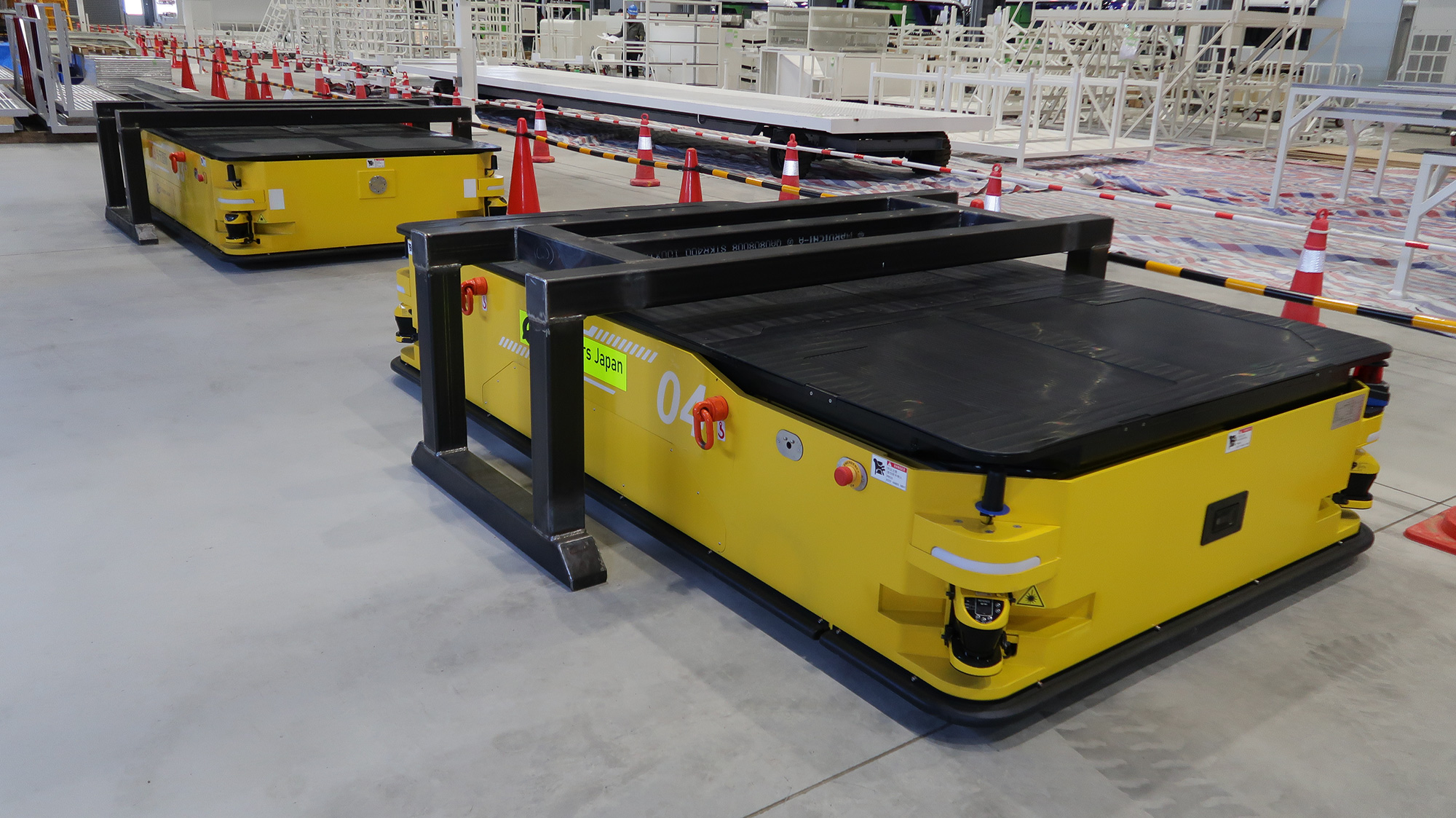
無人搬送車(AGV=Automatic Guided Vehicle)。
2台のAGVは事前に作成した施設内の仮想マップを持っていて、自律走行します。必要な作業現場から呼び出すと、自分で走ってきて搬送し、終われば別の作業場所に行ったり充電場所に移動したりするそうです。ロボット掃除機のルンバみたいです。
ちなみに2台のAGVを同期して大きなものを動かすような使い方は、日本では初めてとのことです。
このAGVは中国メーカーとの共同開発で製作しました。EVM-Jによれば、2台を同期して使えるAGVを開発してくれるメーカーを日本でも探したそうですが、30社以上に打診してすべて断られたそうです。生産設備は日本のお家芸だと思っていたのですが、ちょっと心配になってしまいます。
最新設備の工場に多くの見学者
最新のAGVは、タイヤが見えないため分厚い台車のようでした。1台で10トン、2台で20トンを運ぶことができます。値段が気になってしまうのですが、さすがに非公表でした。
AGVで車体を移動させるため、組立棟の床はフラットになっています。多くの工場では床にピットと呼ばれる作業用の溝を掘って、下から作業するようになっていますが、ゼロエミッション e-PARKではAGVの上部を上げ下げして作業します。これもe-PARKの大きな特長になっています。
ところで、デバッグ棟では使用する工具の位置をトラッキングして作業に応じた設定をしていましたが、将来的には生産工程でも、同じように工具の管理をしていくそうです。
セル生産方式ではひとつの作業工程でさまざまな工具を使うため、工具の設定がオートマチックになればミスも減るし、効率が向上します。生産工程にこのシステムが入るのは第3期工事完成以降になるそうです。
AGVや作業支援システムなどは、日本では最新式の生産設備と言ってもいいのではないでしょうか。実際、現在でも見学者がとても多いそうです。生産が本格的に始まると、さらに見学が増えそうです。その時には改めて見学したいと思ったのでした。
溶接フリーで車体を組み立てる
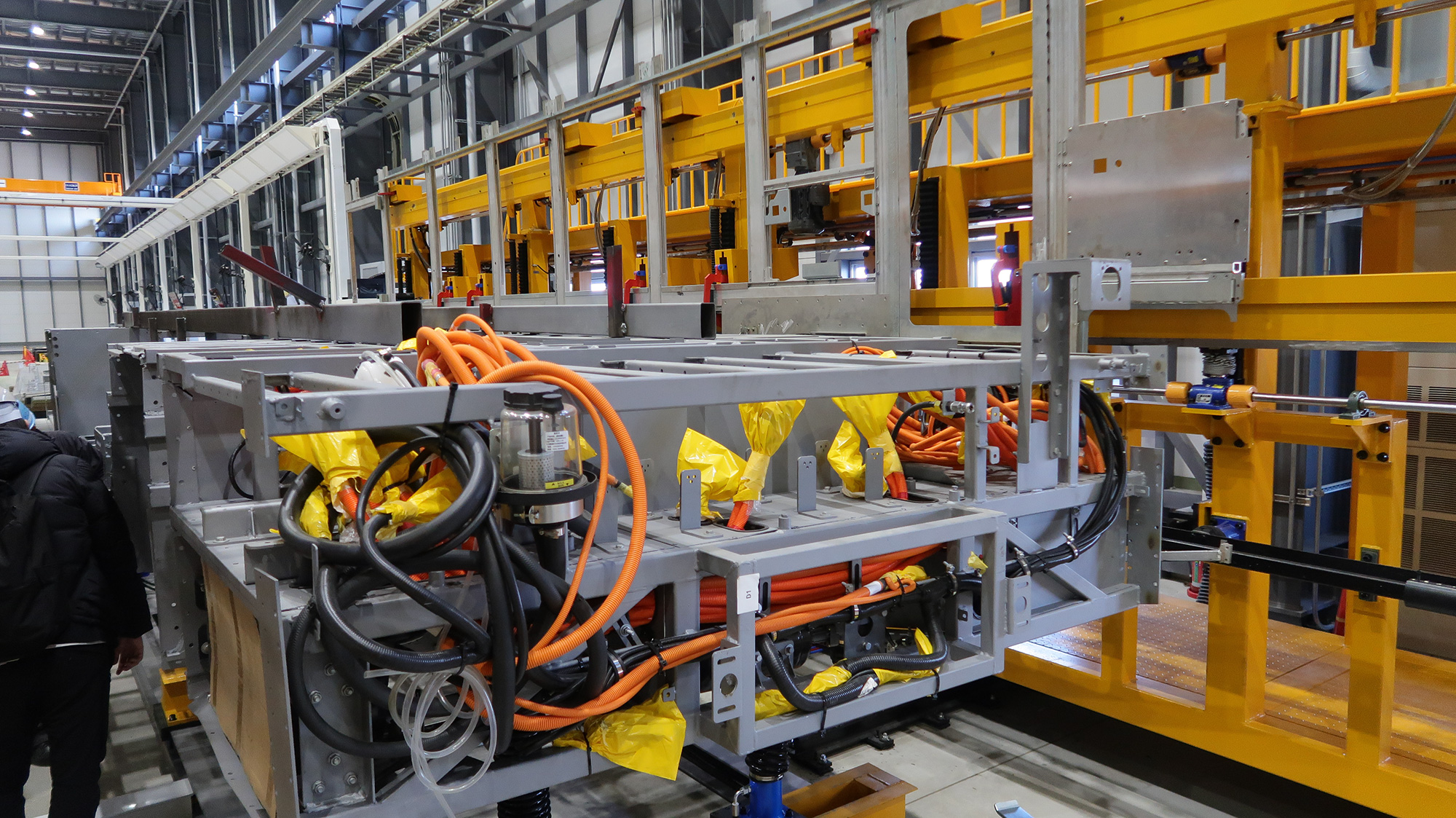
組み立て前のプラットフォーム部分。
現状では、組立ラインを含めて工場の設備としては、全体の半分くらいまでしかできていません。とはいえ作業ができないわけではないので、設置済みの設備を使って徐々にバスの生産を始めていく計画です。
ここでEVM-Jのバスの作り方を簡単に紹介します。バスの車体は屋根、床、前と後ろ、左右のパネルの6面体で構成されています。これを組み立てて立方体にします。ボディーの組み立てはリベット、ボルト、接着剤などで接合する、溶接フリー方式で行います。
見学時には作業前の車体も置いてあったのですが、ぱっと見ただけでは鉄のフレームで作った四角い枠組みにしか見えませんでした。床下部分に配線が走っているのが見えますが、説明を受けるまでバスのシャシーだとは認識できませんでした。
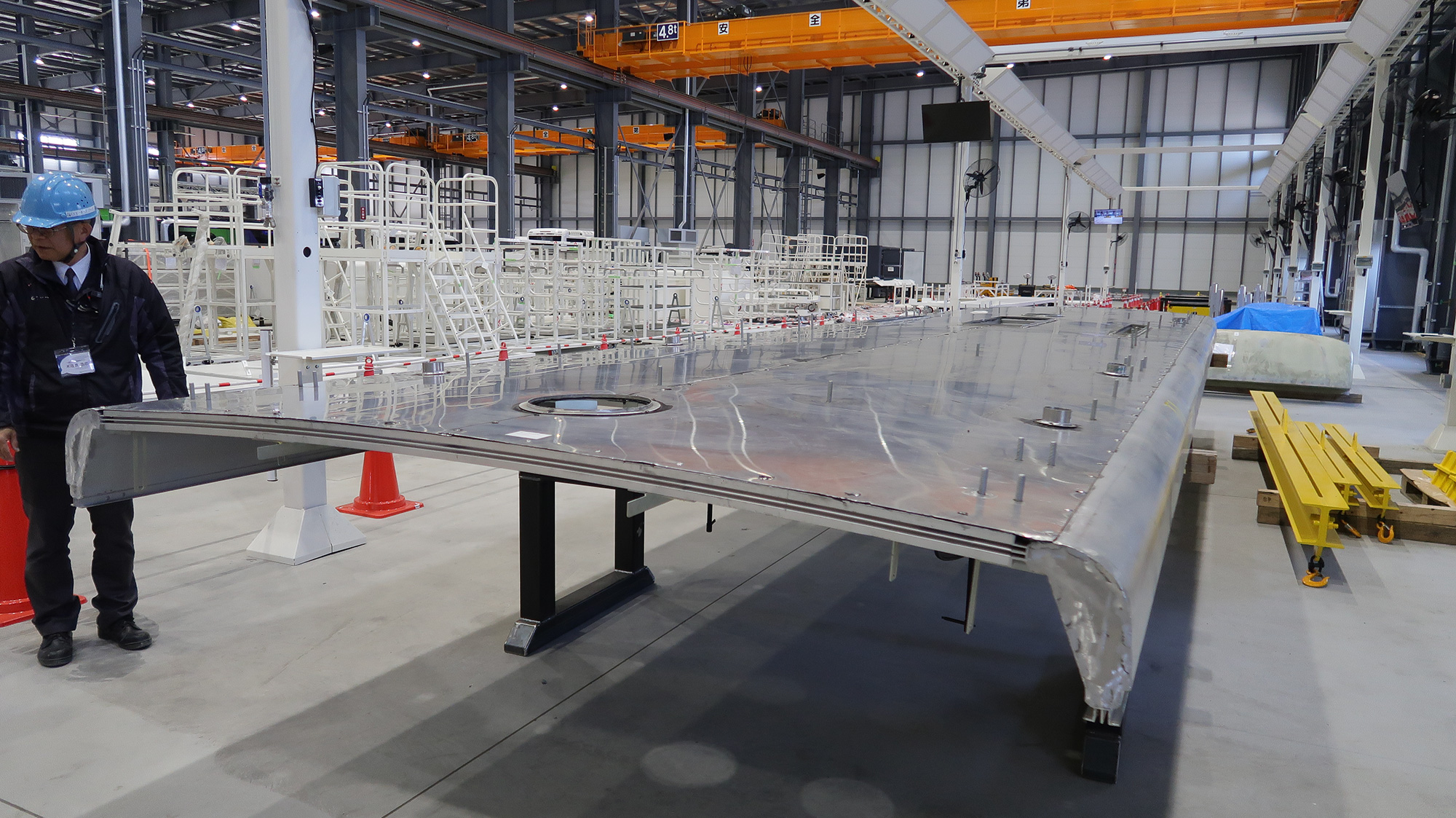
屋根部分のパーツ。この上にもバッテリーなどが搭載されます。
車体が形になったらeアクスルやバッテリー、エアコンなどを含めたシステム、装備を設置します。ただ、床下の配線関係は中国で組み付けています。後から床下で細かい作業をするのは労力がいるので避けたそうです。これらは基本的に手作業です。バスは生産台数がそれほど多くないので、手作りする部分が多くなります。
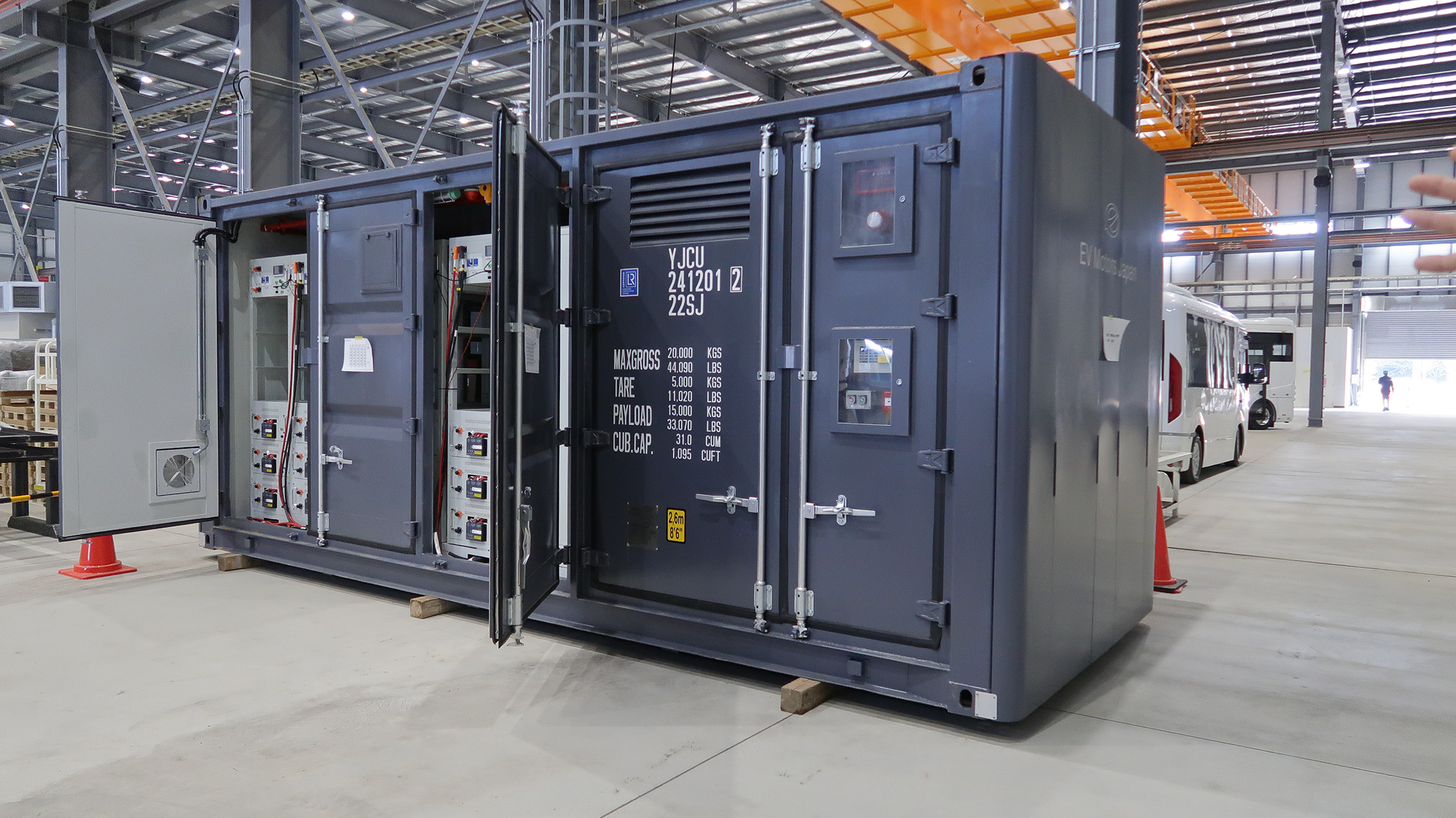
コンテナ型大容量蓄電池。
こうした生産設備の中に、1000kWhの電力を蓄えられるコンテナ型大容量蓄電池がありました。将来的に再エネで工場を稼働させる計画もあるほか、電気バスの納入先でもゼロエミッションに近づけることができるよう、蓄電池のシステムを売っていきたいそうです。
自動車メーカーはお金がかかることを実感
盛りだくさんの工場見学の最後は試運転コースです。組立棟の裏側に完成した試験コースは全長800mで、300mのストレートと、20%勾配の坂道、それに縦揺れ、横揺れ、石畳の3種類の路面を備えた波状路を持っています。
見学時には実際に電気バスでコースを走ってもらうことができました。と言っても自分で運転するわけではないのですが。
走っていただいたのは外周の周回路と坂道を組み合わせたコースです。説明担当のドライバーさんの話では、テストの時にはこのコースを2000kmほど走るそうです。ということは2500周です。目が回りそうです。
大手自動車メーカーや日本自動車研究所のテストコースは1周で数キロメートルありますが、スタートアップ企業でそんな大規模なテストコースを自前で用意することは困難です。でも、短くとも自前の試走路を持っていれば、基本的な車両のチェックは可能です。より本格的な試験が必要な場合はメーカーなどのテストコースを借りればいいわけです。
それにしても、こうして生産現場を見ていくと、改めて、自動車メーカーを立ち上げることの難しさを感じます。生産設備に多額の投資が必要なだけでなく、テストコースにも広大な敷地と設備が必要です。これを全て自前でそろえるのは大変です。それでもEVM-Jは、理想像を目指して、できるところから始めているのだろうなと感じました。
EVM-Jの挑戦は始まったばかりだし、工場が本格稼働するまでにはまだ少し時間がかかりそうです。今は、ゼロエミッション e-PARKから日々、電気バスが出荷されて日本全国を走るようになる日が来ることを期待したいと思います。
取材・文/木野 龍逸
コメント
コメント一覧 (1件)
テスラの日本版となって動きの遅い既存のトラック·バス会社をぶっちぎって欲しいですね!
このジャンルでは水素も有望だと思いますが、兎に角動きが遅い、もっとスピード感を大事にしてほしいものですが
ズッコケると倒産の憂き目を見るので実証実験から先に進めないのでしょうねぇ。